When manufacturing high-precision parts, CNC services deliver consistent, accurate, and efficient results. CNC machines automate various processes like cutting, milling, turning, and drilling, allowing manufacturers to produce parts with intricate designs and tight tolerances. Choosing the right CNC service can make or break your production line regardless of your industry.
There are several CNC processes available, and in this article, we will be going into the 10 best options for CNC precision parts. Each CNC type has its unique features, advantages, and limitations, making it suitable for different materials and applications. We’ll highlight key considerations to help you select the most appropriate CNC service for your project.
Types of CNC Services for Precision Parts
With a wide range of CNC services available, each type offers unique capabilities suited for specific tasks and materials. Here are the top 10 CNC services you can consider:
1. CNC Routing
A CNC router is a computer-controlled cutting machine, offering a modern upgrade to traditional hand-operated routers. This machine operates based on pre-programmed instructions, usually in the form of G-code, which guides its servo motors on how and where to move. The cutting process involves a high-speed rotating tool that carves or cuts material.
CNC routing services
Features:
- Gantry-style design: Supports precise movement along the x- and y-axes for cutting and carving.
- G-code programming: Uses a universal language to control servo motors and cutting tools.
- Automatic tool changers (optional): Allows for seamless tool swapping without manual intervention.
- Limited z-axis movement: Suitable for flatter materials but less effective for deeper cuts.
- Material compatibility: Works best with wood, plastics, foams, and softer metals like brass and aluminum.
Pros:
- Highly efficient for soft material cutting and engraving
- Can produce intricate designs and large cuts
- Suitable for both 2D and 3D carving projects
- Automatic tool changers increase productivity by reducing downtime
- Versatile for applications like woodworking, sign-making, and mold patterns for casting
Cons:
- Limited z-axis movement restricts its ability to cut deeper into thick materials
- Less precise than CNC mills for highly detailed or fine metalworking tasks
- Not ideal for very hard materials like steel or titanium
2. CNC Milling
This is a subtractive manufacturing process that begins with a 3D CAD (Computer-Aided Design) model of the final part. The machine’s table holds the workpiece while a rotating cylindrical tool called a milling cutter removes material. Depending on the part’s complexity, the machine can move along multiple axes to achieve different cutting angles. CNC milling is known for its precision, with machines capable of achieving tolerances as tight as +/- 0.001 inches to +/- 0.005 inches, and even finer tolerances in some cases.
Features:
- High precision and accuracy: Capable of producing parts with tolerances as tight as 0.0005 in, ensuring exact replication of designs.
- Multi-axis movement: Allows for intricate and complex part designs by cutting from different angles.
- Compatibility with various materials: Can work with metals, plastics, composites, wood, and glass.
- Automated tool changes: Some CNC mills feature automatic tool changers (ATCs) for faster and more efficient production.
Pros:
- Increased accuracy and precision
- Fast and efficient production
- Wide material compatibility
- Multi-axis capabilities
Cons:
- Material wastage
- High maintenance costs
- Expensive equipment
3. CNC Lathe Machining
The process starts by clamping the material or workpiece in the lathe’s spindle. As the spindle rotates the workpiece, a stationary cutting tool is used to shape the material. The lathe can perform both Outer Diameter (OD) and Inner Diameter (ID) operations, making it suitable for machining cylindrical parts like shafts and pipes.
Features:
- Rotating workpiece with stationary tool: The workpiece rotates while the cutting tool remains stationary, making it ideal for machining CNC precision parts with cylindrical symmetry.
- 2-axis operation: Standard CNC lathes typically operate on two axes, allowing for basic turning and shaping tasks.
- Turret for tool holding: The cutting tools are mounted on a turret, holding up to 24 tools, depending on the machine.
- Advanced models with multiple axes: Some lathes feature 3-axis or more for additional machining operations like milling and drilling.
Pros:
- Perfect for cylindrical parts
- High precision
- Multi-functionality
- Increased productivity
Cons:
- Limited to rotational parts
- Cost of advanced models
- Less flexibility for non-turning tasks
4. CNC Turning
This is another subtractive machining process where the workpiece rotates while a stationary cutting tool shapes it. The turning machine holds the raw material in place using a chuck, spinning it at high speed. As the material rotates, a single-point cutting tool moves along the workpiece, gradually removing material to form the desired shape. It is ideal for creating symmetrical shapes and parts with round cross-sections, such as tubes, shafts, and rings.
CNC turning operation
Features:
- Rotating workpiece: The workpiece spins at high speeds while the cutting tool remains stationary, shaping the material through contact.
- Precise control: Computer control allows for meticulous precision, producing CNC precision parts with high accuracy and repeatability.
- Versatile material compatibility: CNC turning works with a wide range of materials, including metals, plastics, and composites.
- Supports various shapes: While it excels with cylindrical parts, CNC turning can also handle square or hexagonal raw materials.
Pros:
- High accuracy and precision
- Improved flexibility
- Efficient and fast
- Consistent production
- Safe operation
Cons:
- High initial costs
- Size limitations
- Material wastage
5. CNC Swiss-Type Machining
Unlike traditional lathes, where the workpiece is held stationary while the cutting tool moves, a Swiss-type lathe feeds the workpiece through a guide bushing. This bushing provides support very close to the cutting tool, allowing for enhanced stability during machining. Modern Swiss CNC machines often include multiple spindles and tool paths, allowing simultaneous operations such as drilling, turning, and milling.
Features:
- Guide bushing support: The material is held close to the cutting area, reducing deflection and enhancing precision.
- Multiple spindles and tool paths: Swiss machines can perform simultaneous operations, reducing cycle time for complex parts.
- Automation: Swiss CNC lathes can operate with minimal manual intervention, increasing efficiency and consistency.
Pros:
- High precision and tight tolerances
- High repeatability
- Efficient for complex parts
- Reduced deflection
- Higher RPMs
- Fewer secondary operations
Cons:
- Bar stock limitations
- High tooling costs
- Heat dissipation
- Long setup time
6. CNC Laser Cutting
This versatile technology uses a concentrated laser beam guided by computer instructions to cut or engrave materials. It is especially effective for creating intricate shapes and designs that would be difficult or impossible to achieve manually. It is widely employed in the automotive, aerospace, electronics, medical, and construction industries.
Features:
- Higher Quality Edges: The non-contact nature of the laser reduces the risk of mechanical distortion, resulting in clean, smooth edges with minimal burring.
- Narrow Kerfs: CNC laser cutters produce smaller cut widths (kerfs) than traditional methods, enabling intricate cuts and maximizing material utilization.
- Smaller Heat-Affected Zone (HAZ): Due to the highly focused laser, the heat-affected area around the cut is minimized, reducing material distortion and preserving the integrity of the surrounding material.
Pros:
- High precision and accuracy
- Reduced waste and contamination
- Lower maintenance needs
- Lower repair costs
- Enhanced safety
Cons:
- Difficulty with reflective materials
- Material thickness limitations
- Limited 3D cutting capability
7. CNC Plasma Cutting
CNC plasma cutting utilizes a high-velocity jet of hot plasma to cut through electrically conductive materials. This process delivers fast, precise cuts to meet the needs of several industries. With applications ranging from fabrication and repair to large-scale industrial projects, CNC plasma cutting has become an essential tool for modern metalworking.
Features:
- High-Speed Cutting: CNC plasma cutters can operate at impressive speeds, enabling rapid processing of materials without sacrificing quality.
- Versatile Material Handling: This method is effective for a variety of electrically conductive materials, including steel, brass, copper, and aluminum.
- Cleaner Edges: The non-contact nature of plasma cutting results in cleaner cuts with fewer imperfections and reduced burring.
- Ability to Create Intricate Designs: The precision of CNC plasma cutting allows for the production of complex shapes and detailed designs.
Pros:
- High efficiency
- Improved cost-effectiveness
- Minimal material waste
- Operator safety
Cons:
- Not suitable for non-conductive materials
- The thickness of materials that can be cut is limited by the power of the plasma cutter
- Creates Heat-Affected Zone (HAZ)
- High initial setup costs
8. CNC Waterjet Cutting
This is a precise and efficient manufacturing process that uses a high-pressure stream of water, sometimes mixed with abrasive particles, to cut through a wide range of materials. In the abrasive waterjet cutting method, water is mixed with an abrasive substance, typically garnet, to cut through harder materials like metal, stone, and ceramics. In contrast, pure waterjet cutting uses only water and is best for softer materials like rubber, foam, textiles, and certain plastics.
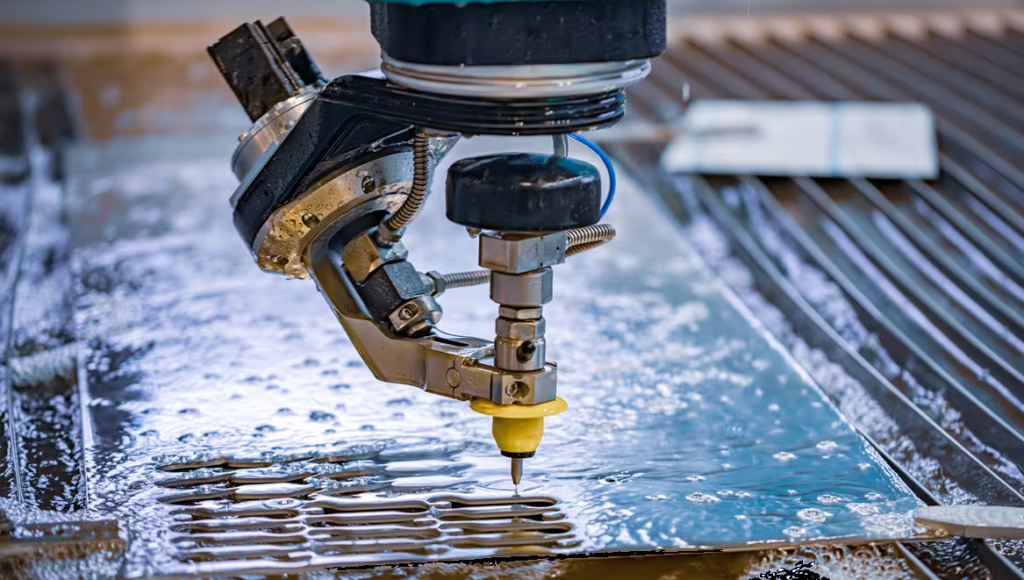
CNC waterjet cutting
Features:
- No Heat-Affected Zones (HAZ): Waterjet cutting does not introduce heat into the material, eliminating issues like warping, melting, or heat-induced stresses.
- Versatile Material Handling: It can cut through almost any material, including metals, stone, glass, ceramics, and composites, as well as softer materials like rubber and foam.
- Extreme Precision: Capable of cutting with tolerances as tight as +/- 0.0003 inches, waterjet cutting excels at intricate and detailed designs.
- Environmentally Friendly: The process uses water and natural abrasives, generating minimal waste and no harmful emissions.
Pros:
- High Precision
- No Material Warping
- High versatility
- No secondary finishing
- Eco-Friendly process
Cons:
- Slower cutting speed
- Higher operating costs
- Limited on softer materials
- Noisy operation
9. CNC Wire EDM Cutting
This non-contact process uses a thin, electrically charged wire to cut conductive materials with extreme precision. The wire does not physically touch the workpiece; instead, it generates electrical sparks that melt or vaporize small sections of the material, allowing for intricate cuts and highly detailed shapes.
Features:
- Non-Contact Process: The wire never physically touches the material, which prevents distortion or stress on the part during cutting.
- Precision Cutting: Wire EDM is known for its high level of accuracy, capable of cutting extremely detailed and intricate shapes with tight tolerances.
- Conductive Materials Only: The process is limited to electrically conductive materials like metals, making it ideal for cutting steel, aluminum, titanium, and other alloys.
- No Burrs or Distortion: Since the material is melted away rather than physically cut, Wire EDM produces smooth, burr-free edges that typically require no secondary finishing.
Pros:
- High precision
- No mechanical stress
- No burrs or secondary finishing
- Continuous cutting process
Cons:
- Limited to conductive materials
- Surface oxidation
- High initial cost
10. CNC Sinker EDM Cutting
CNC Sinker EDM uses electrical sparks to erode material from a workpiece, allowing the creation of complex shapes and blind cavities. Unlike traditional machining, it doesn’t use physical cutting tools or exert mechanical forces. Thus, it is ideal for intricate parts that require precise detailing and cannot withstand the stress of conventional cutting methods. This technique can produce extremely detailed features with tolerances as tight as 0.0001 inches (0.00254 mm).
Features:
- Complex Blind Cavities: Sinker EDM is excellent for creating blind holes, intricate cavities, and irregular shapes that would be difficult to achieve using traditional machining methods.
- Custom Electrodes: The electrode is custom-shaped to match the design requirements of the part, making it versatile for creating detailed molds, dies, and intricate parts.
- Non-Contact Process: Since the electrode never physically touches the workpiece, no mechanical forces are involved, making it ideal for machining fragile or thin materials.
- Dielectric Fluid: The workpiece is submerged in a dielectric fluid that prevents short-circuiting, acts as a coolant, and removes the molten material from the cutting area.
Pros:
- High precision
- Ideal for complex shapes
- No mechanical stress
- Versatile electrode motion
Cons:
- High operational costs
- Limited to conductive materials
Key Considerations for Choosing CNC Service
Choosing the right CNC machining service for your CNC machining project is crucial to ensure high-quality results, efficiency, and cost-effectiveness. Here are the key factors to consider when selecting a CNC process for your manufacturing needs:
Choosing CNC services for precision parts
Material Compatibility
One of the first things to consider is the type of material you’re working with. Different CNC processes are better suited for specific materials like metals, plastics, or composites. Make sure the CNC service you choose can work with your material and can handle its unique properties.
Precision and Tolerances
Some CNC processes, like CNC milling and turning, offer high precision, while others may be more suited for less detailed work. Discuss your tolerance requirements with the service provider to ensure they can meet the specifications without compromising quality.
Complexity of the Design
If your design has complex geometries, undercuts, or intricate details, you need a CNC service that can handle such challenges. 5-axis CNC machining, for example, is ideal for more complex designs, while simpler geometries might only require 3-axis machining.
Production Volume
CNC machining is versatile for both low and high production volumes. However, some CNC services may be more suited to one over the other. For low-volume or prototype production, CNC services that specialize in quick setups and short runs are preferable. For large-scale production, you may want a provider with multiple machines and the capability to handle higher volumes efficiently.
Lead Time and Cost
If you have a tight deadline, ensure the provider can meet it without sacrificing quality. Some providers may offer expedited services, while others may be better suited for longer, more detailed jobs. Always ask about their typical turnaround times for projects similar to yours. CNC machining costs depend on the technique, material, design complexity, machine time, and post-processing requirements. Get detailed quotes from multiple service providers and ensure you’re comparing similar services.
Conclusion
There are many CNC services available for creating precision parts, each with its strengths and applications. Understanding the intricacies of these CNC processes is crucial to selecting the most suitable one for your specific project. Whether you need intricate designs, high precision, or the ability to work with specific materials, choosing the right CNC service ensures better efficiency and product quality. Always work with a reliable manufacturing partner when seeking CNC services near me. This partner will guide you through the process and deliver high-quality results.
Read More: EGERP Panipat Complete Guide: Revolutionising Business Operations in 2024